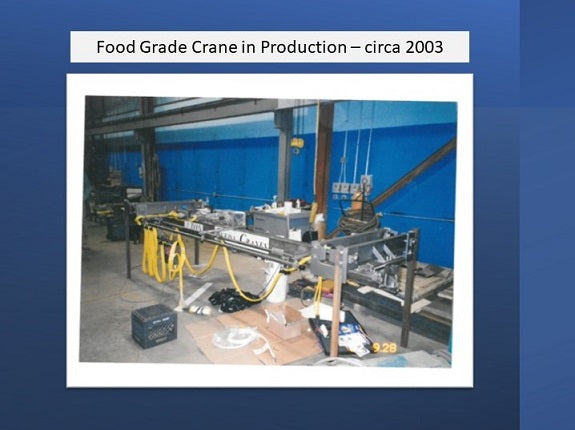
Considerations When Upgrading Hoist Capacity on a Crane Beam
Andrew T. Litecky
Welcome to The Hoist Guy's Blog, where our resident Hoist Guy, Andrew T. Litecky, shares his knowledge and experience of many years in the overhead material handling industry, today to talk about upgrading overhead bridge cranes. Here we’ll look into a case study about some of the challenges one of our clients found when they wanted to upgrade to a higher capacity hoist.
Upgrading the Capacity of a Hoist
What are the main questions to ask when upgrading the capacity of a hoist on a crane beam? Read this case study to learn how we met the challenge.
- Will the beam support a higher capacity hoist?
- What higher capacity hoist suits the application?
- Can the new hoist navigate any obstructions on the crane?
The Case: Increase Hoist Capacity from 1 ton to 1 1/2 Tons
This project began as a request for a retrofit. We were contacted by a large food processing company in regard to a stainless steel food grade bridge crane we had built for them in 2003. The bridge crane was an underhung type with a 16 foot span and 1 ton capacity, with a 1 ton food grade CM Lodestar Model H and a push trolley. The confined area where the crane had been used was now being repurposed, and the new assignment required an increase in the hoist's capacity to 1 1/2 tons with a motor-driven trolley.
Could the beam support a higher capacity hoist?
To make this capacity increase change, the plant manager hired a licensed professional engineer to do an analysis of the crane system. The engineer needed to consider the lower flange loading and deflection of the runways, the end trucks (Acco MHS brand, 3 ton capacity) and the stress deflection of the crane beam, along with an analysis of lower flange loading. The PE also considered the extra weight and capacity of the new hoist.
The engineering study compiled 38 pages of calculations, diagrams, explanations and proofs, and in the end, the existing crane beam was deemed safe for an increase in capacity to 1 1/2 tons. However, the end-user soon learned this solved only half the problem.
What higher capacity hoist suits the application?
Considering this specialty environment, there were few options to replace the existing food grade hoist and meet the newly required 1 1/2 ton capacity. Shupper-Brickle proposed a CM Lodestar, large frame Model R rated with electroless nickel plated load chain. And to meet the customer's spec, we performed the service of disassembling the hoist and sending the components out to be nickel plated as well (this coating is preferred in food and clean production areas because of its ability to withstand wash downs). The painted gearbox and motor would be covered in a stainless steel guard, and the new stainless chain container would be supplied as a large diameter, shorter length stainless steel container. All components were reassembled before turn-key installation.
Can the new hoist navigate obstructions on the crane?
After sourcing the hoist, a question remained: Could it fit on the same crane beam with the same clearances as the original hoist? This was to become the biggest challenge.
The original plain trolley hoist featured a slim profile on both the trolley and the hoist, meanwhile, the new larger frame hoist with a motor driven trolley and a stainless steel guard produced a much wider profile. To achieve the same pick points, the new system had to:
- Avoid the existing stainless steel crane control box on one side of the bridge
- Clear the food grade crane drive units on both ends of the crane
- Allow movement of the motor driven trolley and stainless steel cover despite blockage by power and control festooning and a festooned pendant.
The Resolution: Value-Added Engineering
We found the solution lay with in-house customization of the hoist's configuration. To cover all the pick points and clear obstructions, Shupper-Brickle provided value-added engineering to reconfigure the hoist so that the stainless steel control enclosure fell below the crane drives. Meanwhile, we lengthened the stainless steel festoon cross arms so the festooning cleared the motor drive trolley. Upon completion, a satisfied customer had a 1 1/2 ton capacity crane system that functioned better than the original.
Custom Crane & Material Handling Engineering Services
Since 1969, Shupper-Brickle Equipment has provided overhead material handling equipment and engineering innovations to the Mid-Atlantic States and worldwide. From complete analysis and custom design of bridge cranes and overhead material handling systems to modernization, upgrades and repairs, our innovative engineers can solve any lifting problem, no matter how unusual or unique. Contact us for all your overhead material handling solutions.